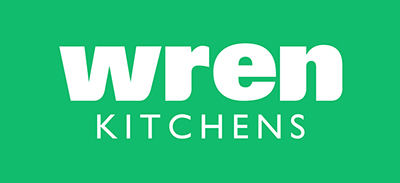
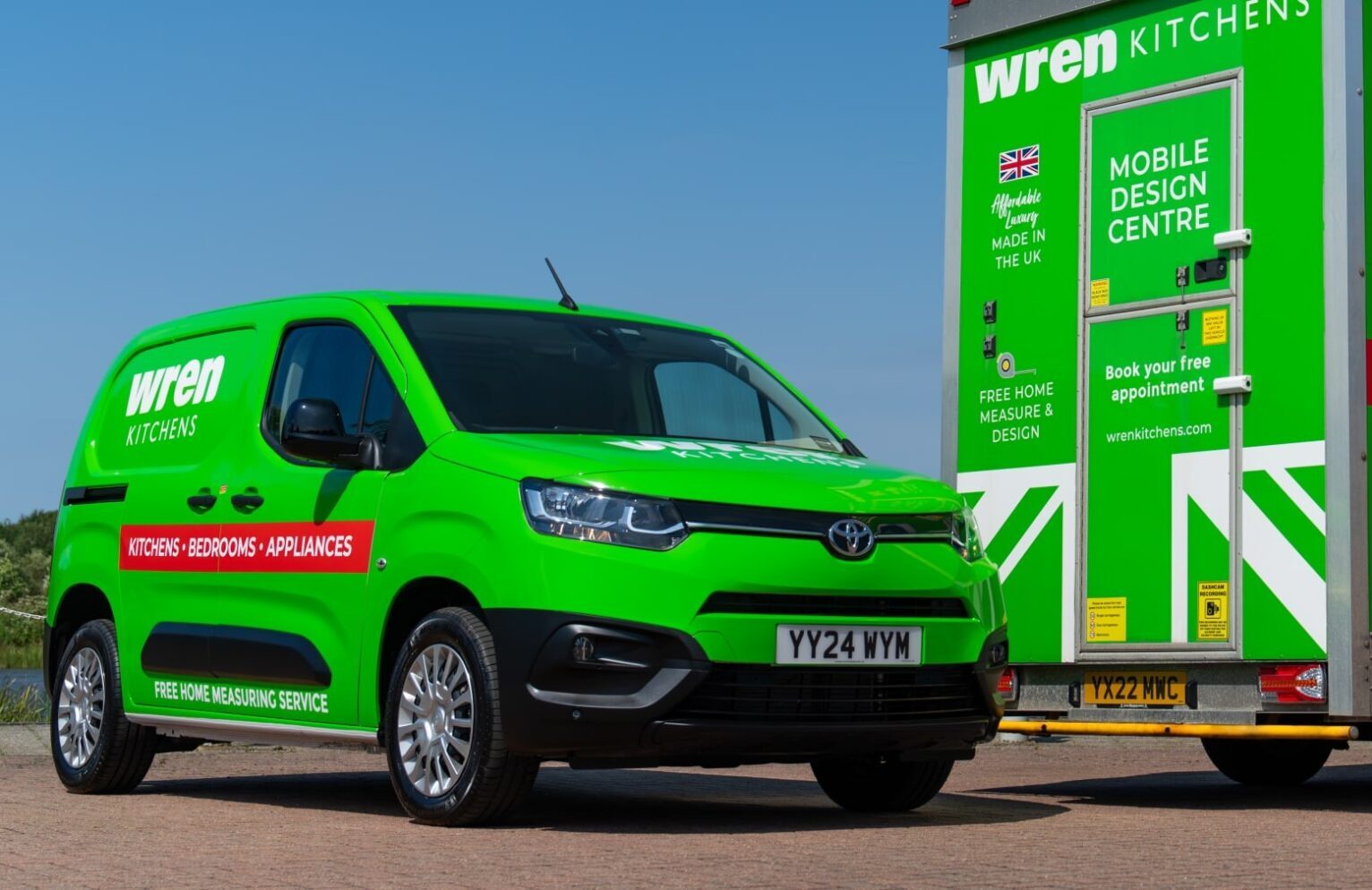
Fleet Size
280 HGVs
570 LCVs
174 company cars
Wren Kitchens is a leading provider of bespoke affordable kitchens. A family-owned firm, it has been trading for 35 years, and has seven depots and 120 showrooms around the UK. The company has been on a sustained journey to lower its fleet risk, and has had great success in driving down both collisions and injuries.
Summary of Achievements
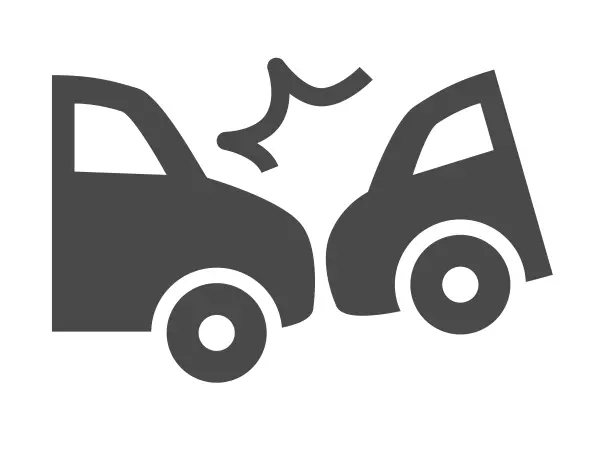
Injury incidents
DOWN 75%
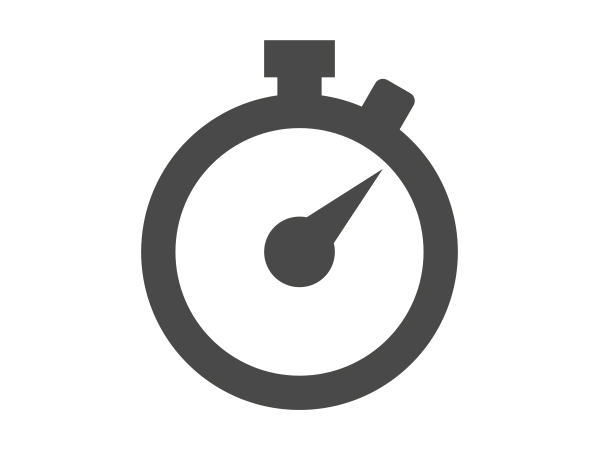
Incident reporting time
DOWN 51%
Demonstrating leadership in driver safety
“Road safety is vital for our business because it protects our employees, the public, and our reputation. A safe transport operation reduces accidents, minimises downtime, and ensures the efficient delivery of our services to our customers.
Tragically, we have experienced first-hand the devastating impact of a fatality, and all our key stakeholders remember this difficult time all too well and it is something we never want us or anyone else to go through for that matter. This incident has strengthened our resolve to prioritise safety above all else.
We are committed to being best in class when it comes to road safety, implementing industry-leading practices, advanced training programs, and rigorous safety protocols. Our goal is not only compliance but excellence – fostering a culture where every journey is taken with care and every employee returns home safely. Our dedication to continuous improvement reflects our unwavering commitment to safety, accountability, and the wellbeing of everyone on the road.”
Lee Holmes, Transport and Logistics Director
More details
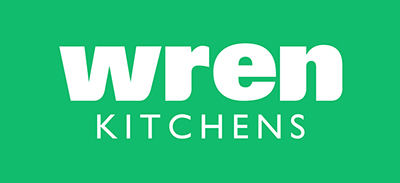
Declaration
“Road safety is vital for our business because it protects our employees, the public, and our reputation. A safe transport operation reduces accidents, minimises downtime, and ensures the efficient delivery of our services to our customers.
Tragically, we have experienced first-hand the devastating impact of a fatality, and all our key stakeholders remember this difficult time all too well and it is something we never want us or anyone else to go through for that matter. This incident has strengthened our resolve to prioritise safety above all else.
We are committed to being best in class when it comes to road safety, implementing industry-leading practices, advanced training programs, and rigorous safety protocols. Our goal is not only compliance but excellence – fostering a culture where every journey is taken with care and every employee returns home safely. Our dedication to continuous improvement reflects our unwavering commitment to safety, accountability, and the wellbeing of everyone on the road.”
Lee Holmes, Transport and Logistics Director
Wren’s HGV fleet carries raw materials, takes product between depots and completes thousands of home deliveries of bespoke kitchens every year. Its LCV fleet is mainly used for surveyors and ‘templaters’ – the employees who measure up prospective kitchen in the early stage of an enquiry.
Vans are also used as mobile showrooms.
The company was recently complemented by its insurer which said it was one of the top firms it worked with in terms of road-risk management. National Fleet Manager, Philip Bennett, and Head of Transport Health and Safety, Tim Pearson, outline what they’ve done to achieve this, in our case study.
Business Benefits
- Personal injury incidents down 75%
- 51% improvement in incident reporting times
Low speed manoeuvring
Driver assistance is a major part of the Wren safety portfolio. The HGVs have seven cameras in total, including forward-facing, side, rear, and driver-facing. Therefore, they have almost a 360-degree view around the vehicle.
However, the company does not rely purely on the cameras. Between half and 70% of all collisions every quarter are low speed manoeuvring incidents, colliding with immovable objects or parked vehicles, usually while reversing. Tim Pearson says that the logistics industry traditionally uses banksmen to guide HGVs into difficult places at low speed; however, he thinks this is problematic as most are untrained, which can make them ineffective as a manoeuvring aid, but also in terms of safety.
He has therefore designed SPOTA training for their HGV teams. SPOTA stands for Stop, Plan, Observe, Talk, Act. Each delivery crew is two-man, one driver and one porter. The porter’s job in SPOTA is to take direction from the driver as to where to stand and exactly what help the driver requires. The porter has two clear signals: arms raised means go, arms crossed means stop. If the driver loses sight of the porter at any point, they stop the vehicle.
Tim says this creates good teamwork between the driver and porter, with a predetermined plan, unambiguous communication and clear protocols.
The SPOTA training has been important for Wren’s fleet as the home delivery environment grows ever more difficult. Phillip Bennett says that over the past 20 years urban roads have become narrower and more challenging for HGV access thanks to the number and size of parked cars outside residences. Since 2021 he believes this has become worse, as more people are home working, post-COVID.
The company has used telematics for several years to track driver performance and location, but more recently it has upgraded its telematics to Samsara, including its AI-enhanced live coaching camera, in its LCVs. It is also considering putting this in its HGVs.
Regular risky driving behaviours are always flagged by its team of driving assessors and the camera footage considered, followed by driver coaching. The Samsara product is also helping, as it alerts the driver to any distraction or inattention in the moment, and this has helped to reduce incidents.
The company is accredited to FORS Gold which obliges them to train drivers in various FORS modules as part of its in-house Driver CPC training, including Safe Urban Driving, and vulnerable road user hazard-awareness courses.
“Ultimately our challenge is human error,” says Pearson. “You can train and manage people and use all the technology, but in the end it comes down to the driver.”
Vehicle safety
The company has Autonomous Emergency Braking Systems (AEBS) fitted to the majority of its HGVs, all its cars and 70% of its van fleet.
“We’ve had three HGV incidents in the past 24 months in which AEBS either has, or would have prevented collision,” says Phillip.
The company is confident that the current generation of AEBS cannot be disabled by the driver, but Pearson says that tampering with any safety equipment would be considered gross misconduct.
Management standards
HGVs and their drivers are far more highly regulated than for smaller vehicles. However, Wren’s senior management doesn’t think this means that LCVs and cars should be managed to a lower standard.
The LCV Risk Steering Group was formed earlier this year. It is trying to ensure management of all vehicles reaches the same standard as for trucks.
This has included bringing the handful of grey fleet vehicles under formal managerial control. Line managers must check the vehicle’s V5, business insurance cover, and MOT, plus counter sign a monthly vehicle check.
Drink and drug testing
Wren uses random drink and drugs testing throughout its HGV teams, including porters and drivers. These tests are stepped up fivefold over the Christmas period.
Until recently drug and alcohol testing of LCV drivers was only post-incident but this is also now being rolled out on a randomised basis.
Human factors
Given that driver error is the biggest cause of incidents, Wren has been working with human factors specialist Dr Lisa Dorn to examine the factors influencing driver behaviour and how the company can create lasting behavioural change.
Projects include:
- Understanding how music affects driving behaviour
- Buddy groups to uncover and explore the issues causing pressure on LCV drivers
- Significant changes to transport planning to remove stress, and the reasons why drivers rush
This last factor has dramatically changed Wren’s approach to HGV job allocation. Previously, although the workload and routes were planned, drivers would be keen to get through their allotted workload as quickly as possible. This introduces greater stress for the driver, and also a higher level of speeding and risky behaviours.
Wren has now amended its planning process so that the drivers cannot make deliveries before the allotted time. It compares planned journey times with actual and is confident that the Paragon planner allows a realistic time interval for journeys, so if drivers arrive early, they must now park up and wait for their delivery window. They cannot leave that site to start the next leg of the journey until the planned time allocated.
This means that drivers have no incentive to rush, either when unloading or driving. The company has had no feedback from drivers as to the effect of this, but the management team is confident that this new adherence to the planned times will remove stress from drivers, and lower the incidence of riskier, fast or aggressive driving.
Post-collision response
Repair costs have risen steeply in the automotive market, and insurance claims are also driven up by third party credit hire vehicles being provided by opposing insurance firms. Wren Kitchens has worked hard to improve its First Notification of Loss response, with drivers responsible for notifying the insurer of any collision within 30 minutes.
This has improved the company’s reporting of collisions and damage, and given it better visibility of overall risk, as well as helping to keep claims costs to a minimum.
In 2021, only 54% of its collision reporting was done the same day; in Q4 2024, this had risen to 82%.
Drivers also receive coaching post-collision, as Tim says this helps to boost their confidence, which inevitably dips after an incident.
It’s also important for continuous improvement. “Although our incidents are almost always low speed and against inanimate objects, it is very important that the driver improves,” he says. “After all, if you’ve hit a gatepost because you couldn’t see it, then you could have hit a child.”